Product Information
FLEXITALLIC UNVEILS NEW OFFSHORE CORROSION SEALING INNOVATION
Flexitallic has unveiled its latest technology innovation, Corriculite, for use in corrosion sensitive applications, including those prevalent in the offshore industry.
A newly-developed gasket filler material, Corriculite tackles the problem of flange face corrosion on bolted joints in seawater and hydrocarbon applications supporting industry’s focus on maximising asset integrity, the extension of equipment life and increased operational productivity. In response to customer demands for an improved material with strong anti-corrosion characteristics, Flexitallic has created the filler material for a range of spiral wound gaskets, specifically designed for use in corrosion-sensitive environments in industries such as oil and gas, power and marine.
Corriculite ensures seals maintain integrity by preventing galvanic corrosion and is Fire Safe to API 6FB. Conventional graphite materials fail to prevent the corrosion of flanges due to graphite’s electrical conductivity and position in the galvanic series. This leads to premature failure and leakage. Corriculite overcomes this issue as it is an inert, non-conductive filler material that remains inactive in corrosive mechanisms and joints. Through rigorous and robust testing, Corriculite is proven to outperform graphite, demonstrating a pressure loss of only one percent, compared to 17 percent in an equivalent graphite gasket.
Corriculite represents Flexitallic’s continual development of new sealing technologies, which includes innovations such as Change™, Thermiculite® and the invention of the original spiral wound gasket in 1912. Since then it has maintained an impressive track record as a disrupting force in its sector with a suite of innovative gaskets and filler materials that meet evolving, industry-driven challenges.
Alex Lattimer Product Line Director at Flexitallic, said: “The development of Corriculite demonstrates the role innovation can play in helping the offshore industries tackle cost and asset integrity challenges. Corrosion is a major issue as joints in seawater and hydrocarbon services are vulnerable to gasket degradation and flange face deterioration. This results in increased costs and lost productivity, as well as safety and environmental concerns, unscheduled downtime and reduced plant availability. “Corriculite will effectively overcome these issues, which will offer significant benefits to industry including cost reduction, improving asset integrity and help maintain essential levels of productivity.”
Download the latest whitepaper
Download our latest whitepaper and find out how Corriculite can help you prevent flange face corrosion.
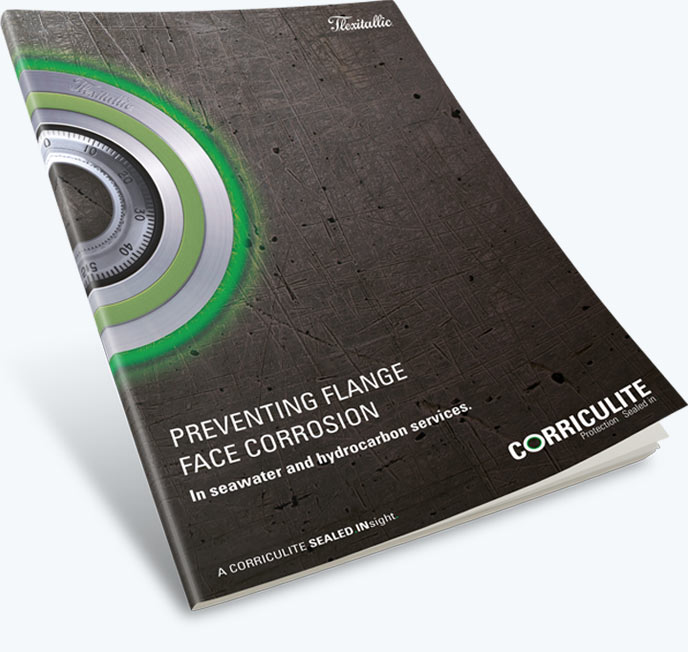
GASKET LEAKAGE TEST: CORRICULITE™ VS MICA
Developed to maximize the integrity of bolted joints in corrosion-sensitive environments, Corriculite combines corrosion prevention and optimum seal integrity. To test Corriculite’s sealing properties Flexitallic ran a leakage test and compared the results with a mica-filled gasket. Watch the video to see the results.
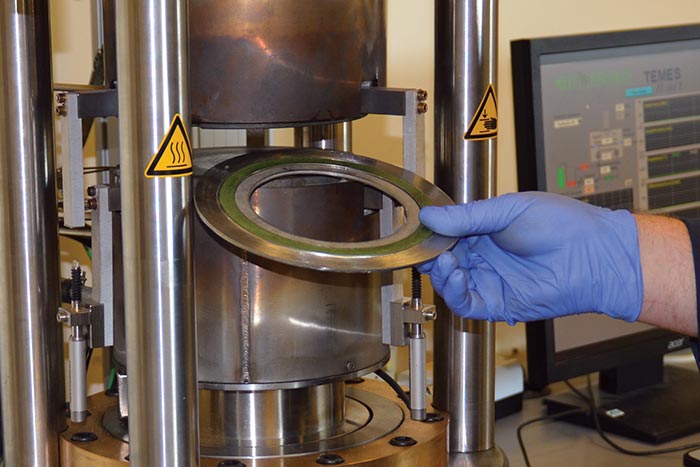
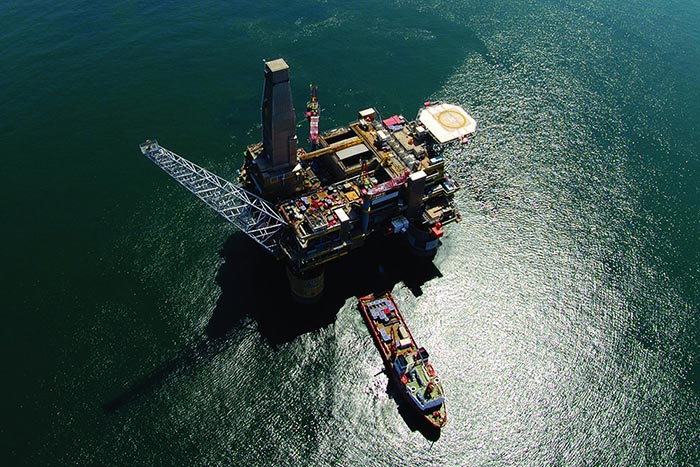
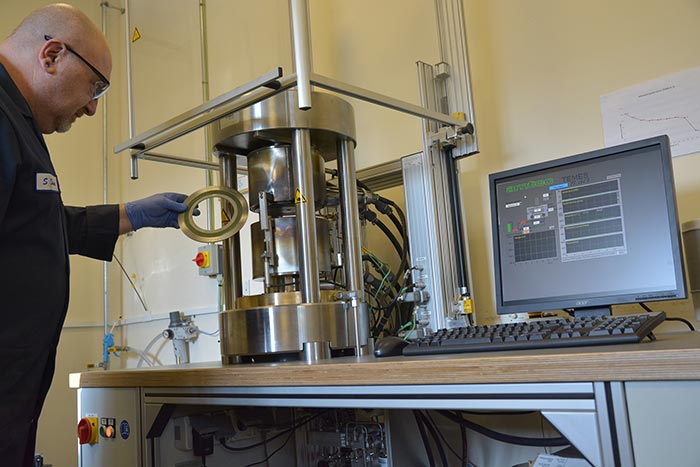